How Cables Are Made – Step 2: Stranding
When producing cables and wires, every little detail counts. In the second part of our series, you will learn how we manufacture stranded conductors.
Once the individual wires have been created through the wire drawing process, they are twisted into a stranded conductor during another process known as stranding. Compared with a solid, single conductor of the same diameter, a stranded conductor is much more flexible and hence less likely to break. The simplest type of stranding is bunch stranding, where individual wires are arbitrarily twisted together. The wires do not have a fixed geometry and their position relative to each other constantly changes over the total length of the strand. The end product is a conductor with a varying cross section and large differences between the position of the widest and the narrowest diameter.
Do you know the conductor classes?
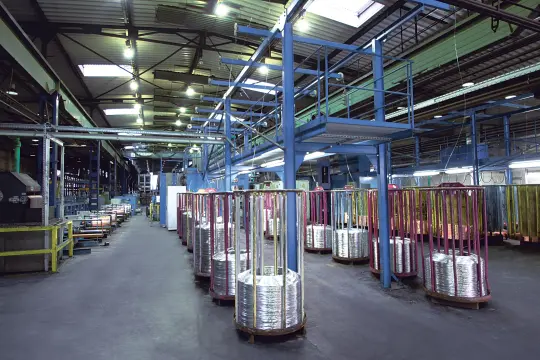
In contrast, the concentric strand is a high-quality and complex type of strand. Here, several layers of wires are twisted around a central wire. Exactly 6 wires fit directly around the central wire to form a conductor with a uniform diameter. Exactly 12 more wires are then twisted around this first layer. The result is a concentric strand with a fixed number of possible wires, i.e. 7, 19, 37, 61, etc., depending on the number of layers. In this type of construction, the relative position of the wires to each other is fixed. The conductor has more or less the same geometry along its entire length and therefore has a very uniform diameter.
Did you know about the conductor classes?
IEC 60228 (DIN VDE 0295) classifies conductors according to their flexibility. Solid, single conductors are assigned to class 1. Stranded conductors are allocated to the other classes. These classes reflect the flexibility of the conductor which increases with the fineness of the individual wires:
- Class 1: solid
- Class 2: stranded
- Class 5: finely stranded
- Class 6: extra finely stranded
ASK THE EXPERT
Mr. Mehl, what do you have to pay particular attention to during stranding?
When making a stranded conductor, the objective is to make it as concentric and compact as possible. The better this is executed, the higher the filling factor and the less unused space between the strands in the conductor. This is best achieved with concentric strands. Once the type of strand has been chosen, various parameters can be tweaked during stranding to modify the quality and features of the final product. For example, both the diameter and flexibility of the strand can be changed by altering the lay length. The lay length is the length of a full rotation around the strand axis. The shorter the lay length, the more flexible the finished strand.
What benefits do concentric strands provide during the subsequent steps in cable manufacturing?
The thickness of the required insulation layer is determined by the strand diameter. The smaller the variation between the narrowest and widest diameter over the total length, the more likely it is that a thin-walled insulation will suffice; this saves material and has the overall effect of making the cable slimmer and more flexible, and thus ideally suited for moving applications.
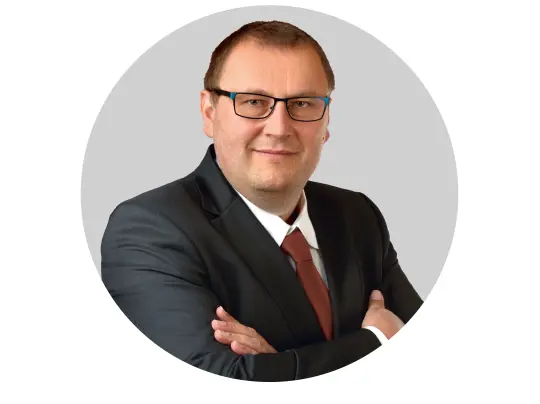