How Cables Are Made – Step 3: Core Insulation
When producing cables and wires, every little detail counts. In the third part of our series, you will learn how we insulate stranded conductors with plastics.
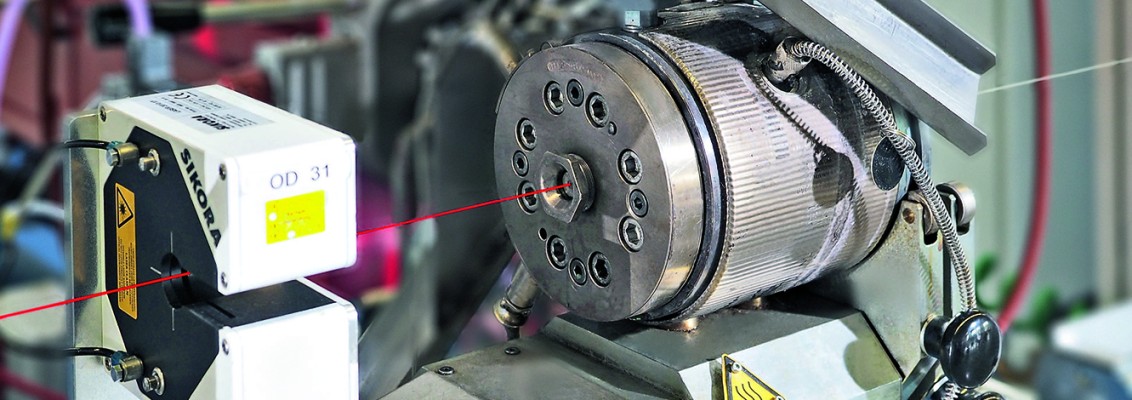
After the individual wires have been stranded to form a conductor, the next step is to insulate it. The purpose of the so-called core insulation is to protect the bare stranded conductor and prevent short circuits inside the cable. Plastics are usually used as the insulating material. Polyvinyl chloride (PVC), polyethylene (PE), and polypropylene (PP) are the most commonly used thermoplastics. Each insulating material has its own maximum voltage and temperature rating. PVC is suitable for most standard cables. If a higher dielectric strength or higher temperatures are required, for example, in motor connection cables, PP or cross-linked polyethylene (XLPE) is the insulating material of choice. With data cables, it is important to keep the loss factor as low as possible. The properties of PE therefore make it a suitable insulating material in such applications. Depending on cable requirements, rubber and silicone elastomers, which are more thermally robust than thermoplastics, can also be used for the insulation. The plastic granules are melted in the extruder and injected around the conductor. Electrical requirements for the cable, such as dielectric strength, determine the minimum wall thickness of the insulating layer. It’s particularly important to ensure the thickness is uniform otherwise short circuits can occur in sections where it is less than the specified minimum because the dielectric strength is too low.
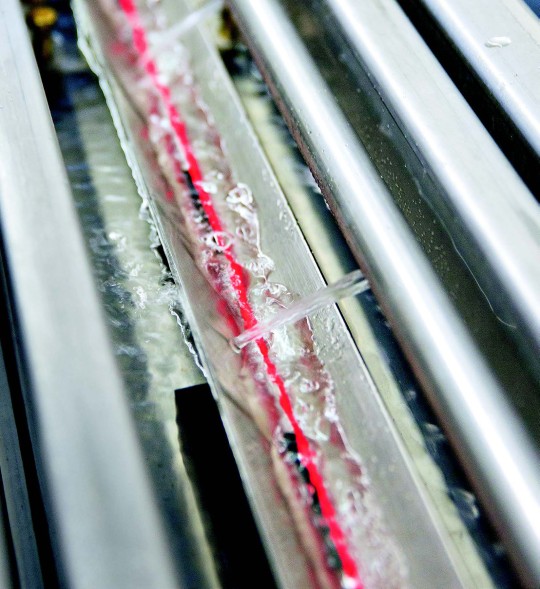
Ask the Expert
A uniformly thick insulating layer is key to high quality cable. How is this guaranteed?
Absolutely concentric positioning of the conductor is essential, and it must be kept in this position during the entire extrusion process. That’s why precision tools must be used to insulate the core. For example, the spray nozzles on the extruder must be machined precisely with virtually no room for error.
Why should the insulating layer be as thin as possible?
Everyone wants a cable that’s inexpensive, space-saving, and lightweight. For this reason, care is taken to keep the insulating layer as thin as possible when insulating the individual conductors. At HELUKABEL, a laser measures the exact outer diameter during the extrusion of the plastic. If necessary, the extruder can carry out an automatic readjustment within a certain range. Nevertheless, random samples are taken from each individual production step and are examined under a microscope for strict quality control.
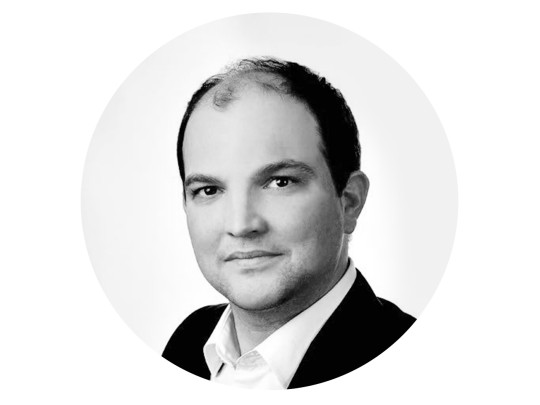