How Cables Are Made - Step 6: Sheath Extrusion
When producing cables and wires, every little detail counts. In the sixth part of our series, you will learn how the sheath is manufactured and why it is important.
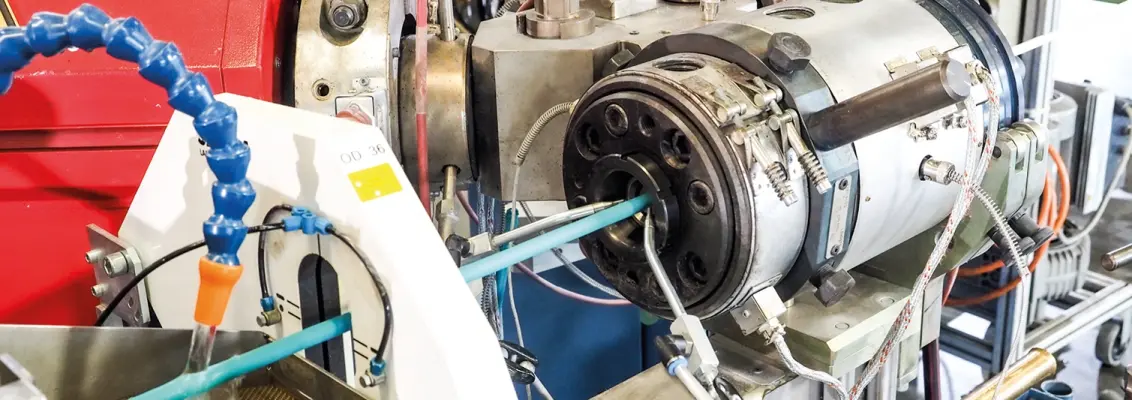
Multicore cables - whether with or without braiding - require a sheath. This is what makes a cable complete, as it holds together its various components such as the cores, braiding and filling materials. But this is not the sheath’s one and only purpose. Sheathing also protects cables from mechanical stresses such as bending and torsion and makes them resistant to heat, cold, fire, chemicals, water or oil.
In order to fulfil the requirements of every application, the right sheathing material must be selected. The range of materials available is wide: in its production facilities, HELUKABEL works with more than 80 different plastics. The most common ones are:
- Polyvinyl chloride (PVC): Often selected for its low cost and overall resistance to chemicals. However, its mechanical resilience is limited, and it is not always oil resistant.
- Polyurethane (PUR): High-quality plastic resistant to abrasion, oil and chemicals, suitable for dynamic applications.
- Thermoplastic elastomers (TPE): Resistant plastics suitable for high mechanical loads and for use in damp and wet rooms.
The wall thickness of the sheath can be between 0.2 and 5 millimetres, but most commonly, it is between 0.8 and 1.2 millimetres. HELUKABEL's thinnest sheathed cables have a diameter of just 2.4 millimetres, while the thickest ones reach a remarkable 78 millimetres in diameter.
Similarly to the core insulation process, the sheath is applied with an extruder. This consists of a metering unit for the plastic granulate, a screw that transports and heats the material, and a cylinder with a spray head that applies the viscous plastic uniformly to the passing cable. Afterwards, the cable runs through a water bath where the sheath cools down and hardens. The sheathed cable is tested with laser cameras and high-voltage testers and finally coiled before it reaches the final step in production: labelling.
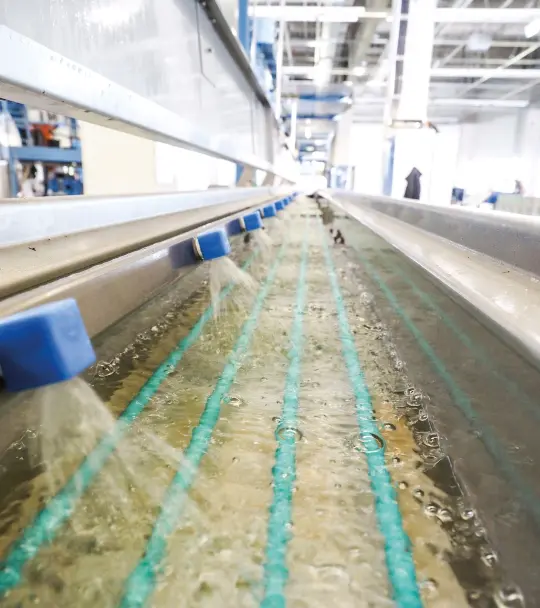
Ask the expert
Mr Sefünc, what is the difference between the core insulation and the sheath?
It’s very simple: The core insulation has the task of galvanically separating the individual elements in multicore cables. It is therefore applied to each core individually and influences the electrical properties of a cable such as the dielectric strength. The sheath, however, protects the inner parts of a cable from harmful environmental impacts as well as from mechanical stress. It has no electrical function. The manufacturing process, though, is the same: both involve a thin layer of plastic that is applied with an extruder.
What factors must be considered during the sheath extrusion process?
There are many parameters that have to be considered: for example, the diameter of the cable itself. The thicker the cable, the stronger the sheath must be to withstand all loads. Moreover, the wall thickness must be as uniform and concentric as possible to ensure harmonious functioning and machine processability of the cable, for example when stripping.
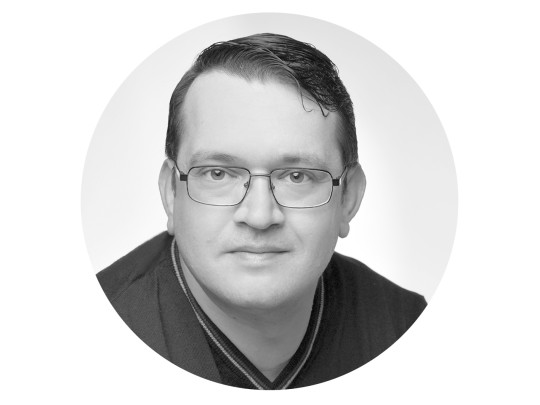
How do cables actually get their individual colour?
The colour concentrate in the desired shade is added to the plastic granulate in the extruder's dosage unit. In the screw, under the impact of heat, a homogeneous and viscous mass is formed, which is similar to honey. This is applied using a spray head so that the cable comes out of the machine in the colour ordered by the customer. Almost all imaginable RAL shades are possible. For some materials, special colour batches have to be produced.